The Benefits of Adhesives & Sealants
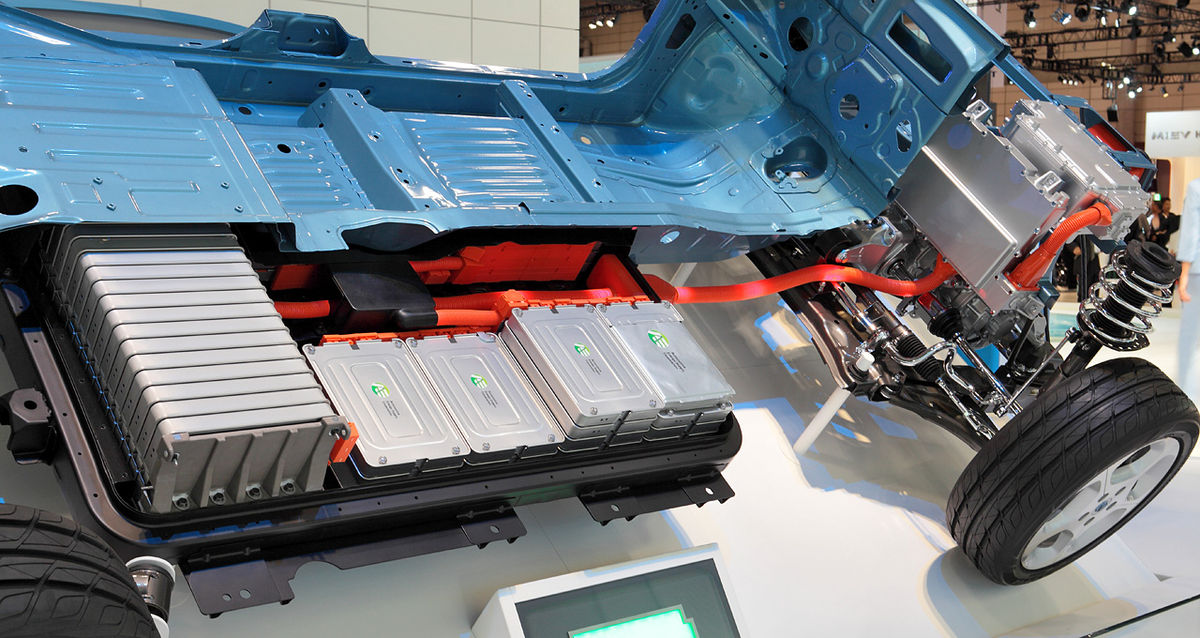
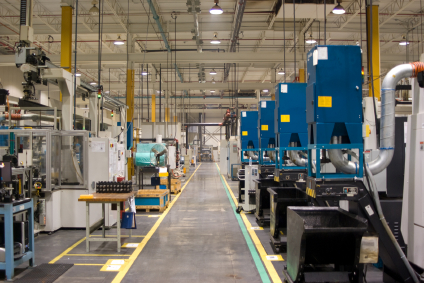
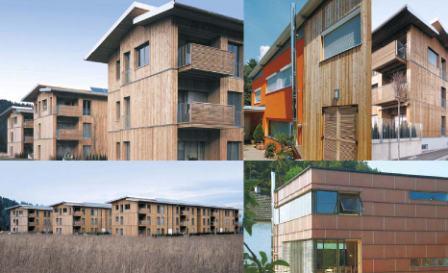
Complex Applications Demand Superior Bonding Solutions…
The development of new materials with diverse applications puts additional challenges on processing technology. This is particularly so when different materials have to be joined to make components which retain their individual beneficial properties in the composite product.
This raises the question: which joining technique is able to join these different materials in such a way that their specific properties are retained?
Traditional joining techniques have well-known disadvantages. With thermal techniques such as welding, the specific properties of the material alter within the heat-affected zone. Mechanical techniques such as riveting or the use of screws in their turn only allow force transfer at points; in addition, it is necessary to drill holes in the work pieces that are being joined, and this “damages” and hence weakens the materials.
In contrast, it is anticipated that bonding technology will assume an ever more important role in industry and the handicraft sector in the future.
There are four key reasons for this:
MATERIAL:
With specialist application, bonding technology can be used to bond virtually any desired combination of materials with each other, creating long-lasting bonds.
PROCESSING:
The use of bonding technology in production processes in general allows the material properties of the substrates to be retained. Compared to welding and soldering/brazing, the bonding process requires relatively little heat input. No damage occurs, unlike when rivets or screws are used.
JOINING:
In product manufacture, the two aforementioned considerations enable the specific material properties of substrates to be optimally utilized in components. This allows new construction methods to be employed.
DESIGN:
It is also possible to use bonding technology to introduce customized additional properties into the component via the actual joining. In addition, the use of bonding technology in industrial production can lead to time savings, can accelerate the production process and hence give rise to specific economic benefits. In shipbuilding, for example, the inside decks can nowadays be bonded into the primary structure, so eliminating time-consuming straightening work that would be required if the inside decks were attached by welding.
Discover the many benefits of adhesives & sealants…
Looking to Source an Adhesive or Sealant for Your Application?
Try the Adhesive & Sealant Council's online Buyer's Marketplace.
This directory tool serves as a quick and efficient way for end users and industry manufacturers to find the right adhesive or sealant solution and the right partner for their application needs. Users can narrow their directory search by market segment, technology, raw materials, equipment or service needs. Try it now.